Stick pack machines are a popular choice for many industries as they provide an efficient way to package powder and liquid products in individual servings.
Due to their convenient size, portability, and ease of use, single-serve packaging is highly sought after by customers.
Manufacturers and co-packers also benefit from stick pack machines and sachet packaging machines as they achieve high production rates and save valuable workplace space.
In this article, we will explain how stick pack machine work, its application, and benefits. Thus to help you get a comprehensive idea about the stick pack machine.
What are stick pack machines
Stick pack machines are a type of vertical form fill seal packaging machine. The process begins with the film being cut and formed into multiple stick packs filled with product.
These bags are sealed vertically very quickly, with speeds of up to 70 bags per minute in each lane. This automated system helps streamline production and ensures that stick packs can be filled and sealed in a short amount of time.
Working process of stick pack machines
1. Film Transporting & Unwinding
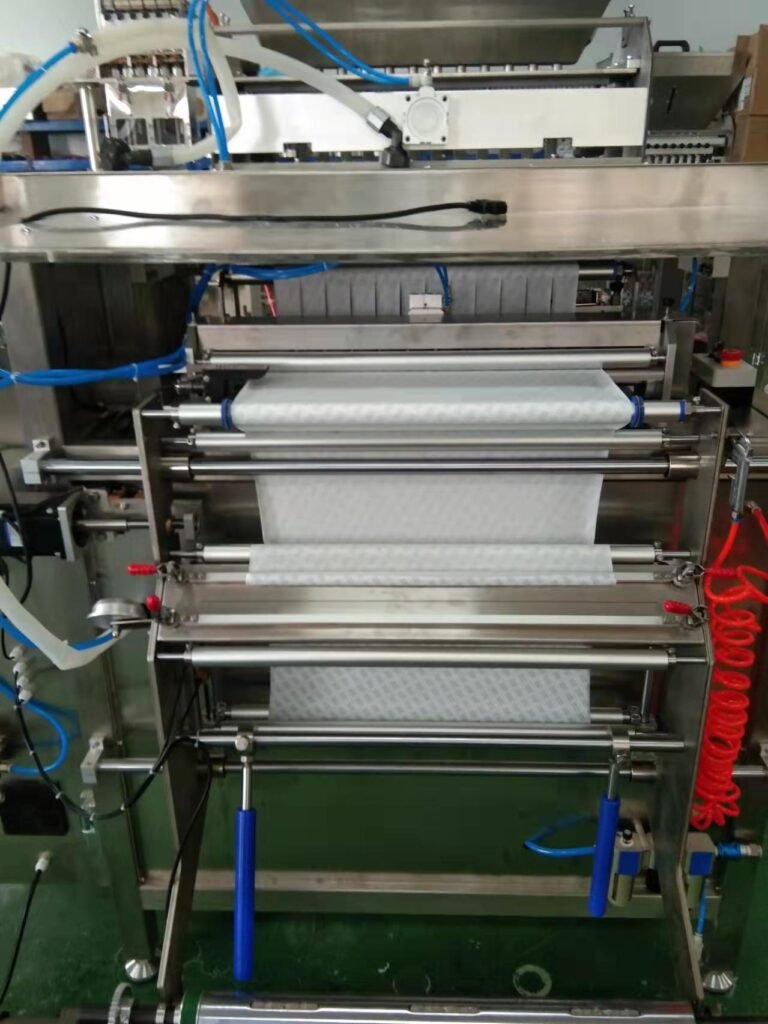
Stick pack machines utilize a single sheet of film material rolled around a core, commonly referred to as rollstock.
The unwinding of the film from the reel is achieved by movement of the cross seal jaws situated at the front of the stick pack machine.
This process facilitates the passing of the film through subsequent stages and eventual wrapping into stick packs.
2. Printing (as an option)
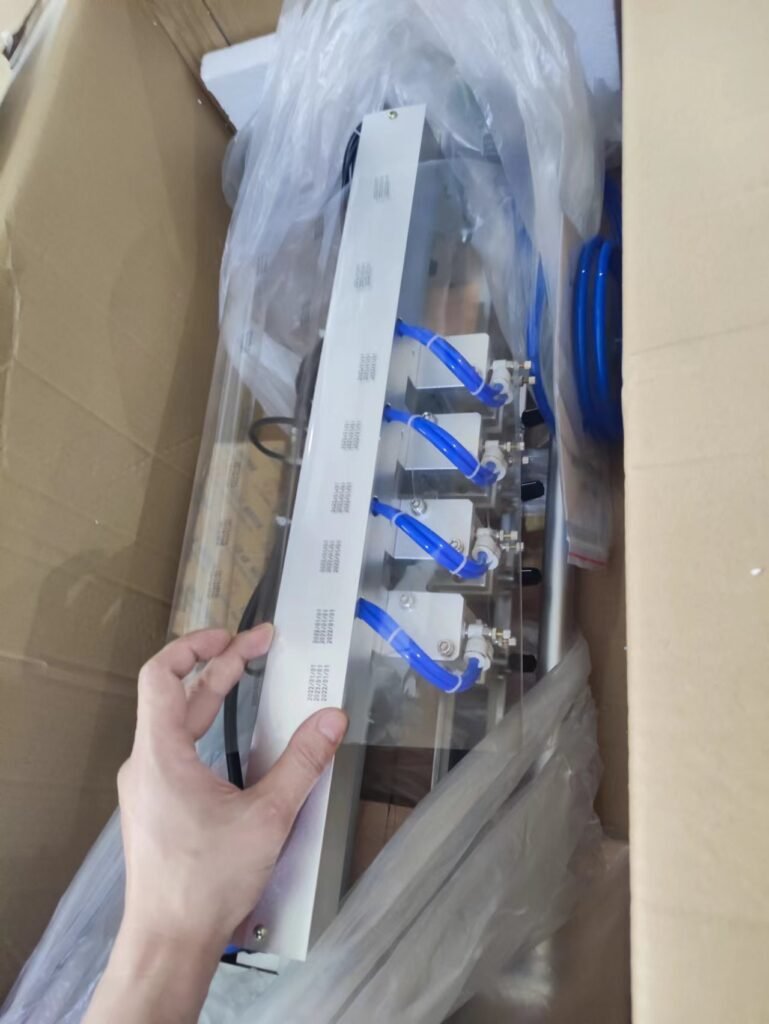
The machine is equipped with a date printing device, and the film passes around a registration roller.
A sensor reads eye marks and adjusts the horizontal seal in relation to the printed material on the film. This ensures that the printed design aligns properly with the sealed area.
The sensor guarantees accurate positioning of each element which results in high-quality printing. It reads the eye marks, and this information is used to adjust the horizontal seal position relative to the ink displayed on the film.
This way, a perfect finished product is achieved every time.
3. Film Tension Control
Next, the film is guided through a series of rollers. These rollers apply even pressure to keep the film at a steady tension which allows the dancer arm to stay in its working position.
As it unwinds, the film passes over a weighted pivot arm at the rear of the machine and moves up and down to remain taut.
An automatic film tracking sensor also ensures that the film will not drift from side to side as it moves along. This maintains its accuracy when going through the machine.
4. Film Cutting
The nip rollers feed the film into the slitter assembly, where it is cut into strips according to the number of lanes in the stick pack machine.
The tension-held film is then passed through sharp knives that interact with a customized roller, slicing it into individual sticks as they are pulled through this device.
The film is then moved through a device that contains blades and a specially designed roller. The pressure created by this apparatus causes the film to be cut into individual stick packs as it passes through.
This process maintains tension throughout and ensures precise cutting of each package.
5. Stick Package Forming
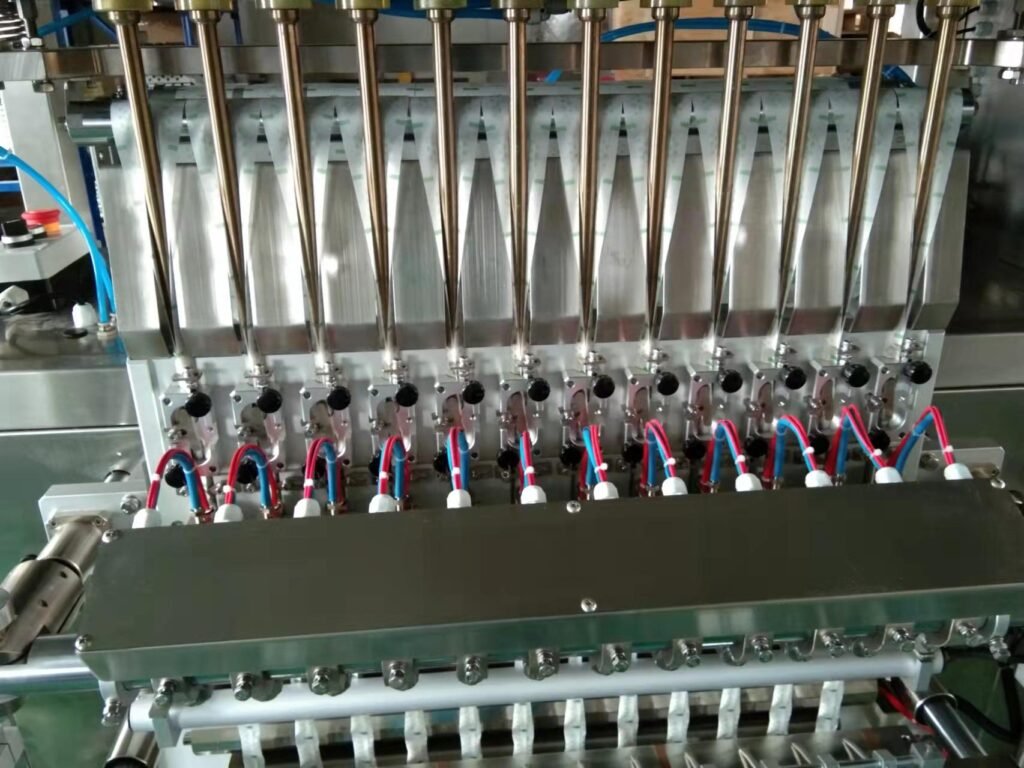
The film is then fed along multiple forming tubes, one for each lane. As the cut film reaches the top of the tube, it is bent around and folded to form a ‘stick pack’ shape. The film’s two edges are overlapped so they can be sealed together. This creates the desired packet shape.
The forming tubes can be adjusted to create a lap seal or fin seal. A lap seal involves overlapping the two outer edges of the film to form a flat surface, while a fin seal lines up the inner sides of the two edges to create an outward protruding finish resembling a fin.
Lap seals generally look more attractive and need less material than a fin seal. Lap seals are generally considered more aesthetically pleasing and require less material than fin seals.
6. Stick Pack Filling and Sealing
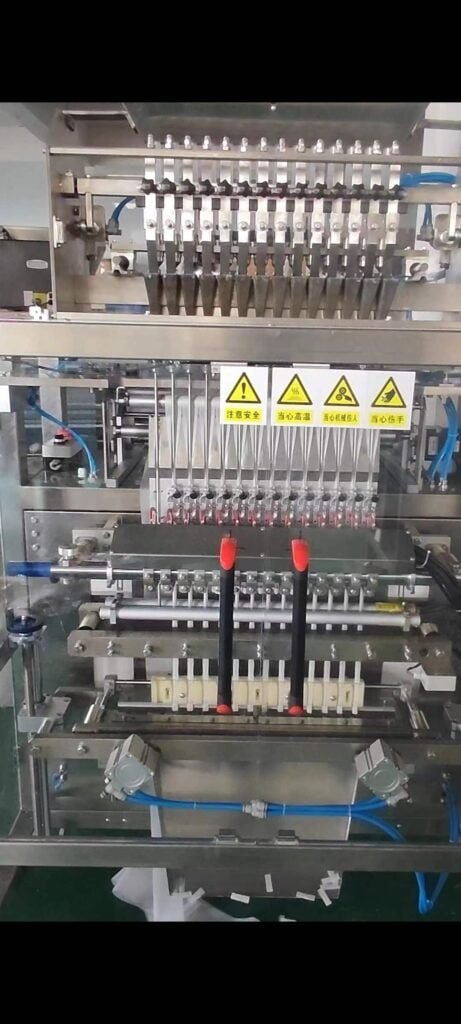
When the film has stopped moving, hot vertical sealer bars move forward and press against the overlapping film. This pressing action creates a vertical seal on the forming tube. The sealer bar is pressed firmly to make sure that the vertical seal is secure.
The horizontal sealing jaw then comes together to make the top seal of one stick packet and the bottom seal of the next one.
While sealed, a filling device such as a volumetric filler, liquid pump or auger filler works to measure and release an accurate amount of product into each individual bag. This product is dropped through the centre of the forming tubes and fills them accordingly.
7. Stick Package Discharge
The product is released into individual stick packs, and the knife blade moves forward to cut the bag or notches the horizontal seal just beneath the horizontal seal jaw.
The completed stick packs are then dropped into an outfeed chute which opens and closes at intervals to drop off the bags. For more precise orientation of stick packs, individual outfeed chutes can be added as an option.
Finally, the bags can be sent to downstream equipment such as carton packing machine or case packing machines etc.
Stick pack packaging machine applications
A stick pack machine is a versatile machine for packaging many different kinds of items. It can be used to package food, beverages, pharmaceuticals, cosmetics, and other consumables.
1.Powder and granular products: Stick pack machines are used for packing powder products, including non free flowing powders and free flowing powders and packing granular products such as coffee, spices, tea, sugar, salt etc.

2.Liquid and paste products: Stick pack machines can also be used for filling liquid or paste type of products like honey, juice, jam, olive oil, drink mixes etc.

3.Medical applications: Stick pack machines are used in pharmaceutical industry for packing of syrups, ointments, pharmaceutical powders and tablets.

4. Food Applications: These machines can be used for packaging sauces, condiments, confectionery items etc.
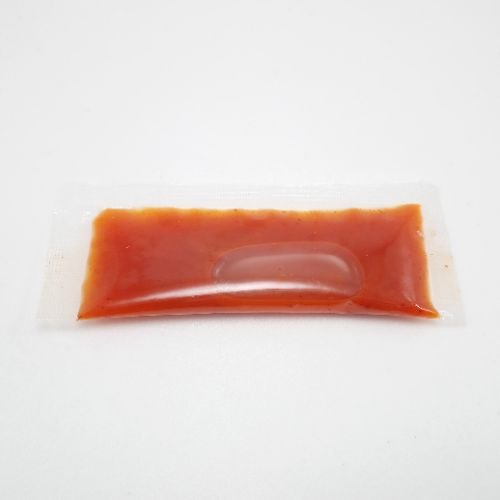
5.Cosmetic applications: Stick pack machines can also package cosmetics like creams and lotion.
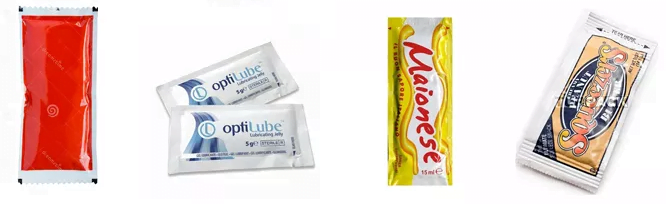
Benefit of stick pack machine
Increased Efficiency: Stick pack machines allow for greater efficiency, as they can quickly and accurately manufacture single-serve packages of liquid, powder or granular products. This allows for high production demand and reduced labor costs.
Reduced Waste: Stickpack machines produce smaller packages that limit the amount of product waste due to overfilling. This helps companies conserve materials and keep production costs low.
Versatility: Stick pack machines are designed to work with a variety of different types of products, including liquids, powders, pastes and granules. This makes them ideal for manufacturing a wide range of products in a single facility without having to invest in multiple machines.
Enhanced Quality Control: Stick pack machines feature precision filling and sealing capabilities that help to ensure product quality. This is especially important for sensitive products, such as pharmaceuticals or food items.
Compact Design: Stick pack machines are designed to be compact and easy to install and operate in a variety of locations. This makes them suitable for use in large-scale production facilities, as well as in small-scale businesses. This makes them an ideal choice for companies on a budget who are looking for efficient and reliable packaging solutions.
Cost Savings: Stick pack machines offer significant cost savings over hand packing, as they can produce more product per hour at lower labor costs. This means companies can save money while still achieving high production rates.
If you are looking to invest in a multilane stick packaging machine to need multiple packaging needs, it is important to take the time to consider all the details.
Planning ahead and understanding the scope of your project can help save money and potential headaches down the line.
To get started on the path to success, Packwaytechno will be your right choice.