Automated packaging equipment has the potential to significantly improve efficiency and productivity in the packaging process, helping businesses to increase their bottom line and remain competitive in an increasingly crowded and fast-changing market. Especially for the food products, frozen foods, pet food products etc.
However, choosing the right automated packaging equipment and maximizing its ROI can be complex, requiring careful consideration of various factors.
In this blog, we will explore the key considerations and strategies for maximizing ROI with automated packaging equipment, including the benefits of automated equipment, the importance of maximizing ROI in the packaging industry, and the steps to calculate the ROI of automated equipment.
Introduction to automated packaging systems ROI
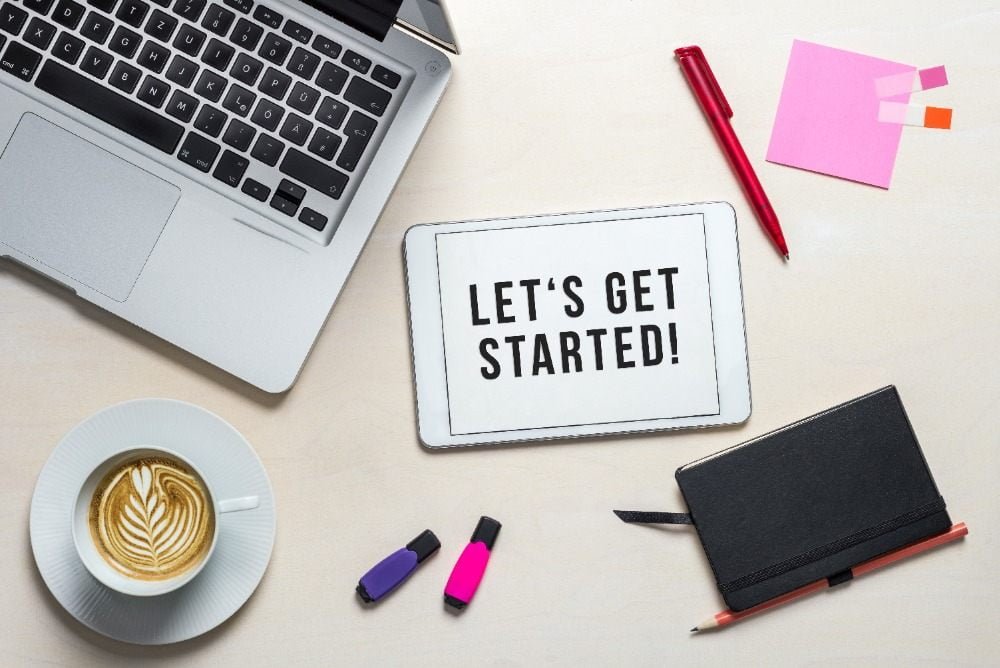
Definition of ROI (return on investment)
ROI also called return on investment, is a financial metric that measures the efficiency of an asset or project. It is commonly expressed as a percentage and is calculated by dividing the net profit generated by the investment by the initial cost of the investment. For example, if you invest $10000 in a project and the net profit is $5000, the ROI would be 50% (5000/10000).
ROI is a meaningful metric for evaluating the potential profitability of an investment or project, as it allows businesses to compare the expected return on different options. It is important to note that ROI is not a guarantee of future performance and should be used as a guide rather than a definitive prediction.
Importance of maximizing ROI in the packaging industry
Maximizing ROI is essential in any industry but is especially critical in the packaging industry due to the high costs associated with equipment, materials, and labor.
In the packaging industry, companies must balance the need for efficient and effective packaging solutions with the need to control costs and maximize profitability.
One way to maximize ROI in the packaging industry is through automated packaging equipment, which can help reduce labor costs and increase efficiency and productivity. Other ways to maximize ROI in the packaging industry include implementing lean manufacturing practices, reducing waste, improving supply chain efficiency, and utilizing cost-effective packaging materials.
By maximizing ROI, packaging companies can improve their bottom line and remain competitive in an increasingly crowded and fast-changing market. Additionally, maximizing ROI can help companies to allocate resources more effectively and make informed decisions about future investments.
Benefits of Automated Packaging Equipment
Increased efficiency and productivity

Automated packaging equipment can significantly increase productivity and efficiency in the packaging process. With automation, packaging tasks can be completed more quickly and with fewer errors, freeing up time and resources for other activities.
Packaging equipment can also operate at a faster rate than manual processes, which can further increase efficiency and productivity. For example, an automated packaging automation line may be able to package hundreds or thousands of products per hour, while manual packaging would be limited to a much lower rate.
In addition, Packaging equipment is typically more consistent and accurate than manual processes, which can lead to fewer errors and rework and further improve efficiency.
Improved accuracy and consistency

Automated packaging systems can improve accuracy and consistency in the packaging process by reducing the potential for human error.
Manual processes can be subject to variations in quality due to factors such as fatigue, distractions, or variations in skill level. In contrast, automated packaging systems are programmed to perform tasks consistently and accurately, with little to no variation in quality.
Reduced labor costs

One of the primary benefits of Packaging equipment is the potential to reduce labor costs. Automated equipment can perform tasks such as filling, labeling, and packaging with minimal human intervention, freeing workers to focus on other operation.
By automating tasks that are time-consuming or require repetitive motion, companies can reduce the need for labor and reduce labor costs. This can be especially beneficial for companies with high labor costs or experiencing difficulty finding and retaining skilled workers.
Moreover, automated equipment can operate continuously without the need for breaks or rest periods, further increasing efficiency and reducing labor costs.
Enhanced safety and ergonomics

Automated packaging systems can also improve safety and ergonomics in the packaging process. Many manual packaging tasks involve repetitive motions or require workers to lift or handle heavy items, which can lead to musculoskeletal disorders and other injuries. Automated equipment can perform these tasks with minimal physical effort, reducing the risk of injury to workers.
In addition, automated equipment can be equipped with safety features such as guards, sensors, and emergency stop buttons to protect workers and prevent accidents. This can help companies comply with safety regulations and create a safer work environment for employees.
Improved ergonomics can also lead to increased comfort and satisfaction for workers, which can, in turn, improve morale and productivity.
Increased flexibility and adaptability
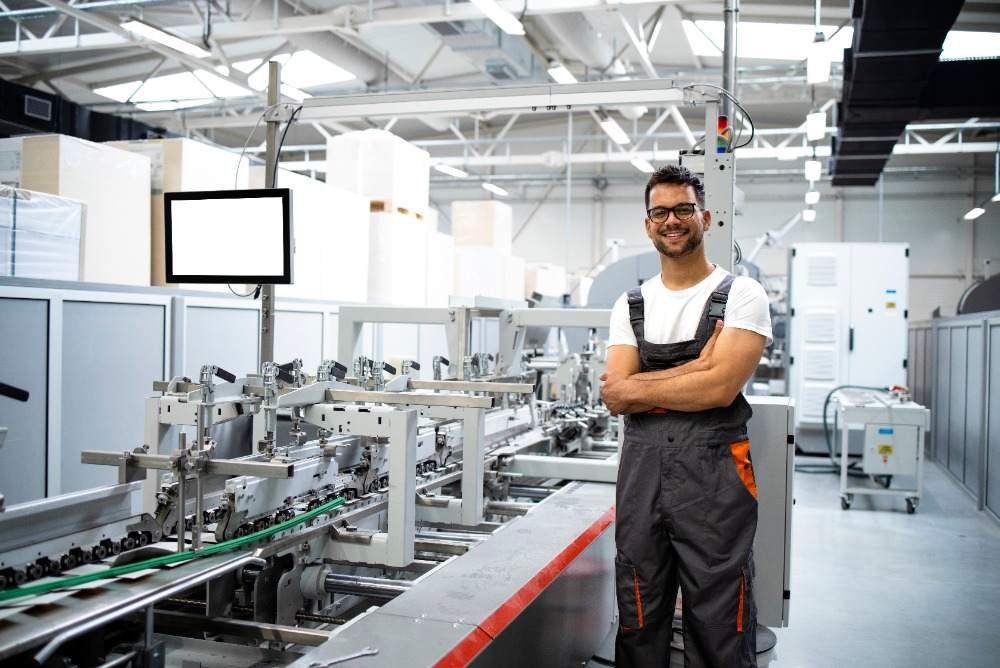
Many automated systems can be easily programmed or reconfigured to handle different products, packaging materials, and production volumes, allowing companies to adapt quickly to changing market conditions or customer needs.
In contrast, manual packaging processes may be more flexible and require significant equipment or procedure changes to accommodate new products or packaging methods.
By providing increased flexibility and adaptability, automated packaging machines can help companies to respond to changing demands and adapt to new market opportunities.
In addition, automated equipment can often be easily integrated with other automation systems and technologies, such as material handling systems and robots, further increasing flexibility and adaptability.
Factors to Consider when Choosing Automated Packaging Machines
Type of product being packaged

The type of product being packaged is a crucial factor to consider when choosing automated packaging machines. Different products may require additional packaging methods and materials, and selecting equipment suitable for the product’s specific needs is vital.
For example, some products may require special handling or protection to prevent damage during packaging and transportation. Others may require precise weighing or labeling to meet regulatory requirements.
Still, others may require specialized packaging materials for temperature-sensitive products, such as custom-shaped or -sized packaging or specialized materials.
Packaging materials and methods

The packaging materials and methods used are also important factors when choosing automated packaging equipment. Different products may require different packaging materials and methods to ensure that they are adequately protected and presented to the consumer.
For example, some products may require packaging materials that provide specific protection or functionality, such as moisture resistance, temperature control, or cushioning. Others may require specialized packaging methods, such as shrink wrapping, blister packing, or flow wrapping.
In addition, it is crucial to consider the availability and cost of packaging materials and any environmental or sustainability concerns. Choosing equipment compatible with a wide range of packaging materials and methods can provide flexibility and reduce the need for multiple pieces of equipment.
Production volume and capacity
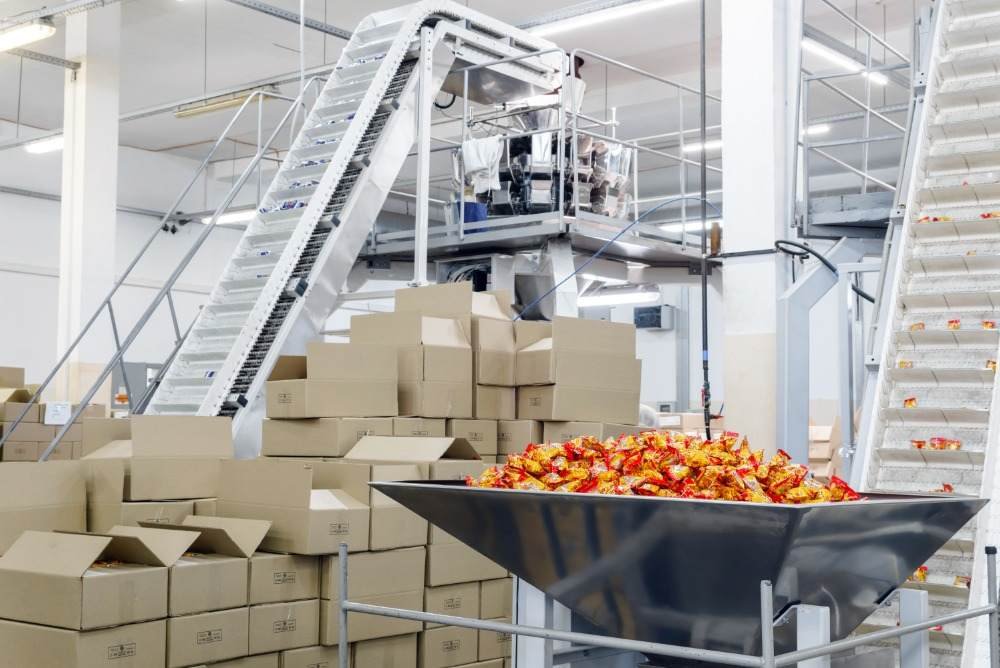
It is important to choose equipment capable of meeting the company’s current and future production needs.
For example, suppose the company is producing a low volume of products but plans to increase production in the future. Choosing equipment with a higher capacity may be necessary to accommodate this growth.
On the other hand, if the company is currently producing a high volume of products but has no plans to increase production, it may be more cost-effective to choose equipment with a lower capacity.
Available space and layout

Be sure to choose equipment that can be accommodated in the available space and is compatible with the facility’s existing layout.
For example, if the facility has limited floor space, it may be necessary to choose compact or modular equipment that can be easily integrated into the existing layout. On the other hand, if the facility has a large, open floor plan, it may be possible to choose larger or more complex equipment that requires more space.
It is also important to consider the location of the equipment within the facility and the materials handling and logistics of the packaging process. Choosing equipment that is easily accessible and can be integrated into the current material flow can help to improve efficiency and reduce the need for additional material handling equipment.
Steps to Calculate ROI for Automated Packaging Equipment
Determine initial investment (cost of equipment and installation)

The cost of automated packaging equipment can vary widely depending on the type and complexity of the equipment, as well as the manufacturer and supplier. It is essential to carefully research and compares different options to ensure that the equipment selected is suitable for the company’s needs and offers a good value.
Installation and setup costs can also vary depending on the equipment’s complexity and the facility’s location. These costs may include installing utilities, such as electricity, and hiring contractors or technicians to install and set up the equipment.
Identify potential cost savings (labor, materials, waste reduction)

Automated packaging equipment can help reduce labor costs by automating tasks that are time-consuming or require repetitive motion, freeing workers to focus on other tasks. It can also operate continuously without needing breaks or rest periods, increasing efficiency and reducing labor costs.
Automated equipment can also reduce material costs by optimizing packaging materials and reducing waste. For example, automated equipment can dispense materials more precisely, reducing the amount of excess material used and waste generated. In addition, automated equipment may detect and reject defective or damaged products, reducing the need for rework and the associated material costs.
Estimate the expected lifespan of the equipment

The expected lifespan of automated packaging equipment can vary widely depending on the type and complexity of the equipment, as well as the manufacturer and the facility’s operating conditions. It is vital to carefully research the equipment’s expected lifespan and consider any warranty or maintenance agreements offered by the manufacturer.
In addition to the equipment’s expected lifespan, it is also essential to consider the potential for upgrades or modifications to extend the lifespan of the equipment. This can improve the ROI of the equipment further and extend its useful life.
Calculate the payback period (the time it takes to recoup the initial investment)

To calculate the payback period, divide the initial investment (cost of equipment and installation) by the annual net profit generated by the equipment. For example, if the initial investment is $100,000 and the yearly net profit generated by the equipment is $25,000, the payback period would be four years (100,000/25,000).
It is important to carefully consider the payback period when choosing automated packaging equipment, as it will impact the overall ROI of the investment. A shorter payback period may indicate a more favorable ROI, while a longer one may indicate a less favorable ROI.
Conclusion
By maximizing ROI, businesses can improve their bottom line and remain competitive in an increasingly crowded and fast-changing market. Automated packaging equipment can help companies to achieve these goals by increasing efficiency, reducing costs, and improving the packaging process.