Dust can be a significant issue in the powder packaging process, causing problems such as contamination, reduced efficiency, and even potential damage to the powder.
Implementing proper measures to eliminate or control dust during packaging is essential. Here are some practical ways to eliminate dust in powder packaging:
Enclosed Sealing Jaw Drives
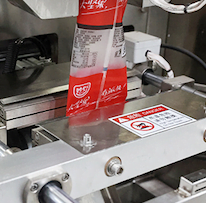
Suppose you are working in a dusty environment or handling dusty products. In that case, ensuring that the moving parts responsible for driving the sealing jaws on your powder packaging machine are protected from airborne particulates is crucial.
These particulates can cause damage or malfunction to the machine if they enter the moving parts. Packaging machines designed for dusty environments often have a completely enclosed jaw drive to address this issue.
This sealed enclosure protects the jaw drive from particulates that could interfere with its operation. By enclosing the jaw drive in this way, the risk of damage or malfunction due to dust or other contaminants is significantly reduced.
As a result, using a packaging machine with a completely enclosed jaw drive can be an effective way to ensure the smooth and efficient operation of the packaging process in a dusty or wet environment.
Additionally, protecting the moving parts of the packaging machinery from dust and other particulates can help extend the machinery’s lifespan and reduce the need for maintenance and repairs.
Dust Proof Enclosures

When selecting packaging equipment for use in a dusty environment, it is essential to ensure that the machinery is adequately protected against dust ingress. No matter what kind of powdered materials are, such as free flow powders, non free flow powders, protein powders, ground coffee or single serving powder etc.
This is especially important for machine enclosures that house electrical or pneumatic components, as dust can interfere with their proper function. To determine the suitability of a piece of packaging machinery for use in a dusty environment, it is crucial to consider its IP (Ingress Protection) Rating.
An IP Rating is a standard that consists of two numbers that indicate the protection level provided by the enclosure against the ingress of dust and water.
The first number represents the level of protection against solid particles, with a higher number indicating a higher level of protection.
The second number represents the level of protection against water, with a higher number indicating a higher level of protection.
When purchasing packaging equipment in a dusty environment, choosing machinery with an IP Rating suitable for the specific application is important. This will help ensure that the machinery is adequately protected against dust and other contaminants and help ensure its smooth and efficient operation.
Dust Suction Device

Dust ingress into the packaging machine is one of many issues to consider when working with dust in the powder packaging process.
If dust finds its way into the package seams, it can interfere with the proper adhesion of the sealant layers in the film during the heat seal process. This can lead to the need for rework or the generation of scrap, which can be costly and inefficient.
To address this issue, a dust suction device can be used at different points in the packaging process to remove or recirculate dust, reducing the likelihood of particulates ending up in the package seals.
By utilizing a dust suction device at various stages of the packaging process, it is possible to significantly reduce the dust present and lessen the risk of dust interfering with the heat seal process. This can help improve the packaging process’s efficiency and reliability while protecting the packaged products from contamination by dust.
Overall, dust suction equipment can reduce dust and other contaminants in the powder packaging process.
Static Elimination
While feeding plastic packaging film through a packaging machine, static electricity can be generated, causing powdery or dusty products to adhere to the inside of the film. This can result in the product being present in the package seals, which can compromise the integrity of the package.
A static elimination bar can be incorporated into the packaging to address this issue. By neutralizing static charges, the static elimination bar can help to prevent the sticking of powder or dust to the inside of the packaging film, improving the overall quality and reliability of the packaged product.
Dust Cup

Automatic pouch filling and sealing machines often incorporate a dust cup above the product dispensing station.
This component is designed to collect and remove particulates as the product is dispensed into the pouch from the filler. The dust cup is positioned above the product dispensing station, allowing it to capture and remove dust and other small particles before they can enter the pouch or interfere with the sealing process.
The use of a dust cup can be an effective way to reduce dust and other contaminants in the pouch filling and sealing process. By collecting and removing particulates as they are dispensed into the pouch, the dust hood helps to prevent contamination of the packaged product and improve the overall quality of the package.
Additionally, by reducing the amount of dust present in the packaging process, the dust cup can help to protect the machinery and improve the efficiency and reliability of the packaging process. Overall, incorporating a dust hood in an automatic pouch filling and sealing machine can be a valuable strategy for reducing dust and other contaminants in the packaging process.
Vacuum Pulling Belt Powder Packaging Machinery

Vertical form fill seal machines typically use friction pull belts to pull the packaging film through the system. These components rely on friction to perform their function.
Still, in a dusty packaging environment, airborne particulates can get between the film and the friction pull belts, reducing their effectiveness and causing them to wear out prematurely.
An alternative option for powder packaging machines is using vacuum pull belts. These components perform the same function as friction pull belts but use vacuum suction instead of friction.
This helps to negate the negative effects of dust on the pull belt system, improving the performance and lifespan of the belts. While vacuum pull belts may be more expensive upfront, they generally need to be replaced less frequently than friction pull belts, especially in dusty environments.
Overall, using vacuum pull belts in a powder packaging machine can effectively reduce the negative impacts of dust on the pull belt system and improve the efficiency and reliability of the packaging process. While the initial cost may be higher, the reduced need for replacements can help to offset this investment over time.
Preventive Maintenance For Machine
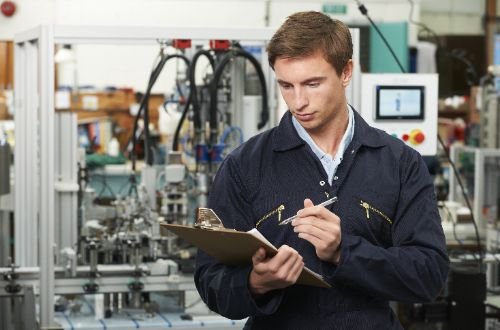
Implementing measures to control dust in the powder packaging process can effectively reduce the negative impacts of particulates on the machinery and the packaged products.
However, following a proper preventive maintenance schedule for the packaging machinery is also important to ensure its smooth and efficient operation.
Many preventive maintenance tasks involve cleaning and inspecting components for residue or dust. These tasks can help to prevent the build-up of dust and other contaminants within the machinery, which can interfere with its performance and shorten its lifespan.
By regularly performing these maintenance tasks and following a comprehensive schedule, it is possible to keep the packaging machinery in good working order and extend its lifespan.
Overall, combining dust control measures and a proper preventive maintenance schedule can be a powerful strategy for reducing the negative impacts of dust in the powder packaging process.
By taking these steps, it is possible to improve the packaging process’s efficiency and reliability while protecting the machinery and the packaged products from the negative effects of dust and other contaminants.
Conclusion
In conclusion, dust can be a significant issue in the powder packaging process, but it can be effectively eliminated or controlled through a combination of the above measures.
By implementing proper dust control measures, it is possible to improve efficiency, reduce contamination, and extend the life of the machinery.
It is essential to carefully consider the specific needs of the product and packaging needs to determine the best solution for reducing dust in the powder packaging process.